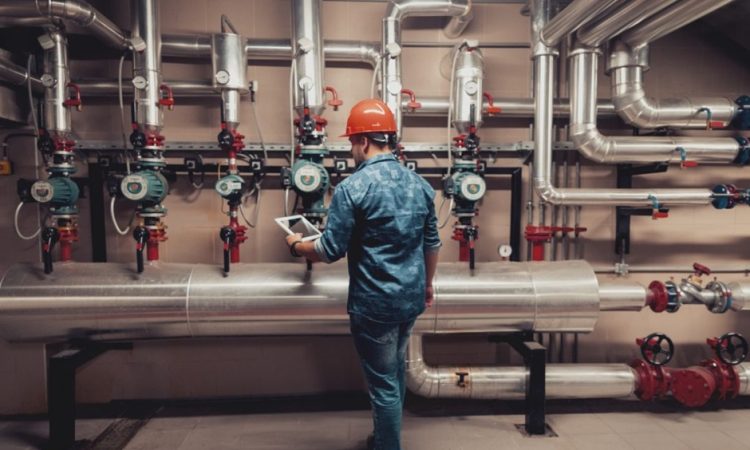
Industrial facility plumbing plays a critical role in the overall functionality and safety of manufacturing and processing environments. Given the complexity of operations and the potential for significant risks, it is imperative for facility managers and decision-makers to prioritize the efficiency and safety of their plumbing systems. This article outlines essential considerations for industrial facility plumbing to ensure that systems operate smoothly while safeguarding workers and the environment.
Understanding the Unique Needs of Industrial Plumbing
Industrial facility plumbing differs significantly from residential plumbing due to the scale, materials, and regulatory requirements involved. Industrial facilities often handle larger volumes of water, chemicals, and waste products. Consequently, the plumbing systems must be robust enough to accommodate these demands. Key considerations include:
- Pipe Size and Material: Industrial plumbing typically requires larger diameter pipes made from durable materials such as PVC, stainless steel, or carbon steel. The choice of materials should be based on the type of fluids being transported, temperature ranges, and potential corrosive effects.
- Flow Rate and Pressure Requirements: Understanding the flow rate and pressure requirements for various processes is crucial. Industrial plumbing must ensure adequate water supply and pressure for machinery, cooling systems, and other operational needs.
- Waste Management Systems: Industrial facilities generate significant amounts of waste, including hazardous materials. Effective plumbing solutions must incorporate waste management systems that comply with environmental regulations and prevent contamination.
Compliance with Regulatory Standards
Compliance with local, state, and federal regulations is a fundamental consideration in industrial facility plumbing. Regulatory bodies such as the Occupational Safety and Health Administration (OSHA) and the Environmental Protection Agency (EPA) set standards that impact plumbing systems. Facility managers should ensure that:
- Permits and Inspections: All plumbing installations and modifications meet regulatory requirements and undergo necessary inspections. This includes obtaining permits for construction and ensuring compliance with plumbing codes.
- Regular Audits: Conducting regular audits of plumbing systems helps identify potential issues before they escalate. This proactive approach not only ensures compliance but also enhances the overall safety and efficiency of operations.
Incorporating Advanced Technology
In today’s fast-paced industrial environments, incorporating advanced technology into plumbing systems can significantly enhance efficiency and safety. Facility managers should consider the following technologies:
- Smart Monitoring Systems: Implementing smart monitoring systems can provide real-time data on water usage, flow rates, and system pressure. This technology enables early detection of leaks and inefficiencies, allowing for timely interventions.
- Automated Control Systems: Automated control systems can optimize water distribution and usage, reducing waste and ensuring that systems operate within desired parameters. These systems can adjust water flow based on demand, enhancing both efficiency and sustainability.
- Preventive Maintenance Software: Utilizing software solutions for preventive maintenance helps facility managers schedule inspections and repairs effectively. This proactive approach minimizes downtime and extends the lifespan of plumbing systems.
Ensuring Worker Safety
Safety is paramount in industrial environments, and plumbing systems can pose various risks if not properly managed. Essential considerations for ensuring worker safety include:
- Regular Training and Awareness: Providing regular training to employees on plumbing system operations, potential hazards, and emergency procedures is vital. Employees should be aware of how to identify signs of plumbing issues, such as leaks or unusual odors, and know how to report them promptly.
- Emergency Response Plans: Developing comprehensive emergency response plans that include plumbing-related incidents is crucial. These plans should outline procedures for handling leaks, spills, or other plumbing failures, ensuring that employees know how to respond quickly and effectively.
- Protective Equipment: Ensure that employees working in or around plumbing systems are equipped with appropriate personal protective equipment (PPE). This may include gloves, goggles, and protective clothing to minimize exposure to hazardous materials.
Regular Maintenance and Inspections
A well-maintained plumbing system is essential for operational efficiency and safety. Regular maintenance and inspections should include:
- Routine Inspections: Conducting routine inspections of all plumbing components, including pipes, fittings, valves, and fixtures, helps identify wear and tear, corrosion, or potential leaks. This proactive approach reduces the risk of costly failures.
- Cleaning and Flushing: Regular cleaning and flushing of plumbing systems prevent the buildup of sediments and debris that can lead to blockages. Implementing a routine flushing schedule ensures that water quality remains high and systems operate efficiently.
- Repair and Replacement: Addressing plumbing issues promptly is critical. Facility managers should establish a clear protocol for repairs and replacements to minimize downtime and maintain system integrity.
Conclusion
Industrial facility plumbing is a vital component of operational efficiency and safety. By understanding the unique needs of industrial plumbing, ensuring regulatory compliance, incorporating advanced technology, prioritizing worker safety, and implementing regular maintenance, facility managers can create a plumbing system that supports their operations while safeguarding employees and the environment. Prioritizing these essential considerations will lead to improved productivity and reduced risks in industrial facilities.